از آهنگری تا خمکاری: معرفی تمامی روشهای شکلدهی فلزات
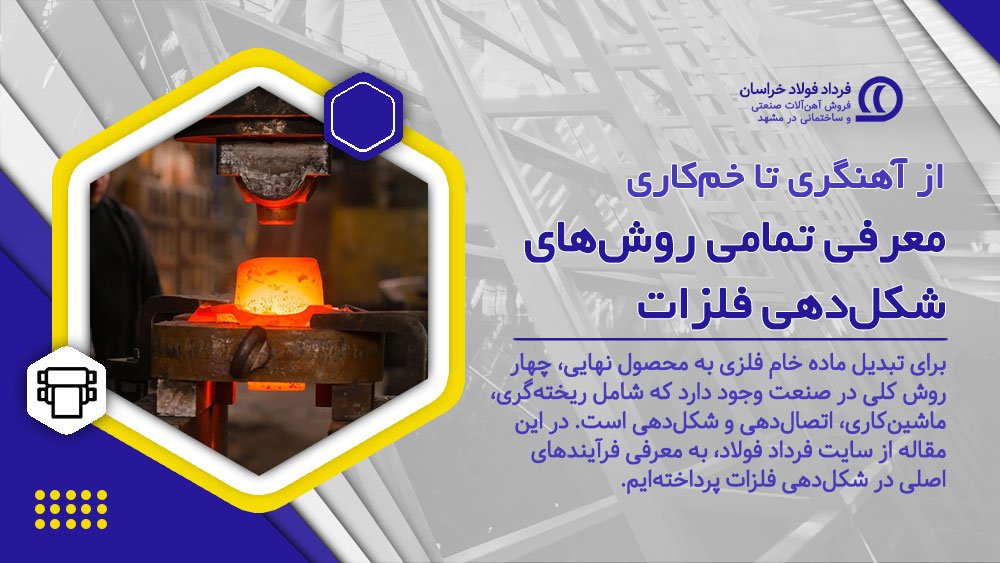
برای تبدیل ماده خام فلزی به محصول نهایی، چهار روش کلی در صنعت وجود دارد که شامل ریختهگری، ماشینکاری، اتصالدهی و شکلدهی است. در این مقاله از سایت فرداد فولاد، به معرفی فرآیندهای اصلی در شکلدهی فلزات پرداختهایم.
معرفی روشهای شکلدهی فلزات
در تولید صنعتی، چهار روش کلی برای ساخت محصولات فلزی وجود دارد: ریختهگری، ماشینکاری (برشکاری، تراشکاری، فرزکاری و ...)، اتصالدهی و شکلدهی. شکلدهی فلزات یک فرآیند مهم در صنعت فلزات است که به منظور تولید قطعات و ساختارهای مختلف از فلزات مورد استفاده قرار میگیرد. این فرآیند از طریق اعمال تغییر شکل پلاستیک (دائمی) به فلزات با استفاده از روشهای مختلفی انجام میشود. به طور کلی، شکلدهی را میتوان در 3 دسته جمعبندی کرد:
روشهای حرارتی
این دسته شامل روشهایی مانند نورد، کشیدن گرم، کشیدن سرد و آهنگری حرارتی است. در این روشها، فلز تحت تأثیر حرارت قرار گرفته که منجر به افزایش انعطافپذیری و تغییر شکل آن میشود.
روشهای سرد
این دسته روشها شامل پرسکاری، آهنگری و همچنین شکلدهی با استفاده از ابزارهای مختلف میشود. در این روشها، فلز در دمای محیط (بدون استفاده از حرارت) شکلدهی میشود.
روشهای پیشرفته
این دسته شامل روشهایی مانند شکلدهی انفجاری و ... هستند که از تکنولوژیهای پیشرفتهتر و دقیقتر برای شکلدهی فلزات استفاده میکنند.
فشار، دما و انرژی در شکلدهی فلزات
در هر یک از این دستهها، فلزات برای شکلدهی به روشهای مختلفی تحت فشار، دما، یا انرژی قرار میگیرند تا به شکل نهایی خود برسند. انتخاب روش متناسب با نوع فلز، شکل نهایی مورد نظر و خواص مورد نیاز قطعه، انجام میشود. در ادامه، چند روش اصلی و رایج در شکلدهی فلزات را بررسی میکنیم.
آهنگری (Forging)
آهنگری یکی از قدیمیترین حرفههای انسانی است که به شکلدهی فلزات با استفاده از ابزارهای دستی و مکانیکی میپردازد. این حرفه از دوران باستان وجود داشته و تا امروز نیز ادامه دارد. آهنگری معمولاً شامل استفاده از ابزارهایی مانند پتک یا چکش، سنبه، ماتریس و دیگر ابزارهای دستی است. این روش معمولاً در تولید قطعاتی با خواص مکانیکی و نیازمند به دقت بالا کاربرد داشته و در صنایعی مانند خودروسازی، هواپیماسازی، صنعت فلزات، و صنایع ساختمانی مورد استفاده قرار میگیرد. در ادامه، به معرفی برخی از فرآیندهای آهنگری در روشهای شکلدهی فلزات میپردازیم:
شکل دادن با استفاده از چکش
این یکی از روشهای اصلی اهنگری است که در آن فلزات به کمک چکش یا پتک شکل داده میشوند. این فرآیند اغلب به صورت دستی صورت گرفته و نیاز به مهارت و توانایی فیزیکی بالایی دارد.
استفاده از سنبه و ماتریس
ماتریسها برای شکلدهی دقیق فلزات به کار میروند. این ماتریسها معمولاً از فولاد ساخته شده و شکلهای مختلفی دارند که با فشار به فلزات، شکل داده میشوند.
مراحل اصلی در فرایند آهنگری
فرآیند آهنگری معمولاً به وسیله یک چکش و یا ماتریس انجام میشود. آهنگری منجر به بهبود خواص مکانیکی فلزات میشود و اغلب برای قطعاتی با خواص مکانیکی بالا استفاده میشود. در ادامه مراحل اصلی آهنگری را مرور میکنیم:
آمادهسازی ماده اولیه
ماده فلزی مورد استفاده برای آهنگری باید به شکل قطعات یا نوارهایی با ضخامت مشخص آماده شود.
گرم کردن فلز
معمولاً قبل از شروع آهنگری، ماده فلزی تا دمای بالا گرم میشود. این پیشگرم کردن، قابلیت شکلپذیری فلز را افزایش میدهد.
چکش کاری
در این مرحله، فلز گرم شده، به وسیله یک چکش و یا سنبه و ماتریس، شکل داده میشود. این فرآیند باعث تغییر شکل فلز و شکلدهی قطعه میشود.
خنک کردن
پس از چکش کاری، قطعه فلزی به طور کنترلشده خنک میشود. این مرحله برای حفظ شکل نهایی و خواص مکانیکی مطلوب، ضروری است.
پردازش نهایی
پس از خنک شدن، ممکن است قطعه فلزی نیاز به کارهایی مانند تمیزکاری، تراش و ماشینکاری داشته باشد تا به شکل نهایی خود برسد.
شکلدهی غلتکی (Roll Forming)
شکلدهی غلتکی یکی دیگر از روشهای شکلدهی فلز و نوعی نورد است که نوارهای فلزی را گرفته، از طریق غلتک استوانهای عبور داده و یک مقطع ایجاد میکند. این فرآیند برای تولید حجمهای زیاد ایدهآل است و میتوان از آن برای شکل دادن به فلزاتی که از استحکام بالایی برخوردار هستند استفاده کرد. محصولات حاصل از شکلدهی غلتکی را میتوان به هر طولی برش داد.
صنایعی که از شکلدهی غلتکی استفاده میکنند شامل خودروسازی، خورشیدی، انرژی، ساختوساز، هوافضا، تهویه مطبوع، لوله و ... هستند. کاربردهای رول فرمینگ عبارتند از تجهیزات ساختوساز، نردبان، تجهیزات HVAC، کشتیها، نرده، قاببندی، آسانسور، پنجرهها، قطارها و لوله.
کشیدن (Drawing)
کشیدن یکی از روشهای مهم در شکلدهی فلزات است که برای تولید قطعات با شکلها و رشتههایی با ابعاد مختلف استفاده میشود. این فرآیند عموماً برای تولید سیمهای فلزی و قطعاتی با سطح مقطع دایرهای مورد استفاده قرار میگیرد. در ادامه، مراحل اصلی کشیدن در روش شکلدهی فلزات را بررسی میکنیم.
آمادهسازی ماده اولیه
ماده اولیه معمولاً به شکل بیلت یا نوارهای فلزی آماده شده و به دقت اندازه گرفته میشود.
گرم کردن
ماده اولیه تا دمای مناسبی گرم میشود تا به وضعیت مناسبی برای کشیدن برسد.
کشیدن
در این مرحله، ماده فلزی گرم و انعطافپذیر کشیده میشود. فرایند کشیدن ممکن است حرارتی (با استفاده از دما) یا مکانیکی (با استفاده از فشار) باشد. ماده فلزی تحت تاثیر قدرت کشش قرار گرفته و به شکل دلخواه کشیده میشود.
خنک کردن
پس از کشیدن، قطعه فلزی به طور کنترل شده خنک میشود. این مرحله برای حفظ شکل نهایی و خواص مکانیکی مطلوب ضروری است.
پردازش نهایی
در انتها، قطعه کشیده شده ممکن است به فراوری نهایی مانند برش، تمیزکاری، و یا سایر فرآیندهای ماشینکاری نیاز داشته باشد.
اکستروژن (Extrusion)
دستگاه اکستروژن یک قطعه فلز را گرفته و آن را از طریق قالب مقطع مورد نظر عبور میدهد تا محصول نهایی تولید شود. در حالی که آلومینیوم فلز اولیه مورد استفاده در اکستروژن است، میتوان از فلزات دیگر نیز استفاده کرد. این فرآیند شکلدهی فلز برای تولید مقاطع پیچیده و اشکال توخالی ایدهآل است. قالبهای مورد استفاده نسبتاً مقرونبهصرفه هستند و استفاده از این فرآیند را در صنایع مختلف از جمله معماری، کشاورزی و حملونقل آسان میکند. نمونههایی از کاربردهای اکستروژن عبارتند از اتصالات، ریل، میلهها، اجزای سازهای، میلهها، قوطیهای آلومینیومی، قابها و لوله.
پرسکاری (Stamping)
پرسکاری یکی از فرآیندهای مهم در شکلدهی فلزات است که برای تولید قطعات با شکلها و سطوح مختلف استفاده میشود. در این روش، فلز تحت فشار قرار گرفته و با استفاده از قالبها و ماتریسها شکل داده میشود. این روش برای تولید اجزای بزرگ با شکلهای ساده تا متوسط مورد استفاده قرار میگیرد. پرسکاری معمولاً در دو نوع سرد و گرم انجام میشود که هر کدام ویژگیها و کاربردهای مختلفی دارند. در زیر، به بررسی مراحل اصلی پرسکاری میپردازیم.
آمادهسازی ماده اولیه
ماده اولیه معمولاً به شکل قطعات فلزی یا صفحات فلزی آماده میشود. این قطعات باید به اندازه و شکل مناسب برای فرآیند پرسکاری آماده شوند.
گرم کردن ماده اولیه (در صورت نیاز)
در برخی موارد، ممکن است نیاز باشد که ماده فلزی قبل از ورود به دستگاه پرسکاری، گرم شود. این کار باعث افزایش انعطافپذیری ماده فلزی و بهبود فرآیند پرسکاری میشود.
پرسکاری
در این مرحله، ماده فلزی تحت فشار قرار گرفته و با استفاده از یک دستگاه پرسکاری و یا ماتریسهای مخصوص، به شکل داده میشود. فشار و دما به صورت دقیق کنترل میشوند تا شکل نهایی دقیقاً مطابق با مشخصات مورد نظر بهدست آید.
خنک کردن
پس از پرسکاری، قطعه فلزی به طور کنترل شده خنک میشود تا به شکل نهایی خود برسد. این مرحله برای حفظ شکل و خواص مکانیکی مطلوب ضروری است.
پردازش نهایی
در انتها، ممکن است قطعه پرسکاری شده نیاز به پردازشهایی مانند تمیزکاری، تراش و ماشینکاری داشته باشد تا به شکل نهایی خود برسد.
پرس هیدرولیکی (Hydroforming)
در این روش، فلزات تحت فشار آب در یک دستگاه پرس هیدرولیکی قرار گرفته و با اعمال فشار هیدرولیکی به شکل مورد نظر درمیآیند. این فرآیند معمولاً برای تولید قطعات با شکلها و ابعاد مختلف و با شکلهای پیچیده بدون نیاز به قالبهای سخت بهکار میرود. در زیر، مراحل اصلی پرس هیدرولیکی در شکلدهی فلزات را بررسی میکنیم:
آمادهسازی ماده اولیه
ماده اولیه، که معمولاً به شکل بیلت یا ورق فلزی میباشد، به اندازه و شکل مناسب برای فرآیند پرس هیدرولیکی آماده میشود.
قرار دادن ماده اولیه در دستگاه
ماده فلزی در دستگاه پرس هیدرولیکی قرار گرفته و مکانیسم هیدرولیکی برای اعمال فشار آماده میشود.
اعمال فشار هیدرولیکی
با اعمال فشار هیدرولیکی، ماده فلزی شکل داده میشود. فشار هیدرولیکی معمولاً توسط یک سیلندر هیدرولیکی ایجاد میگردد که باعث تحرک یک پیستون شده و فشار را به ماده فلزی انتقال میدهد.
خنک کردن
پس از شکلدهی، قطعه فلزی خنک شده و از دستگاه پرس هیدرولیکی خارج میشود. این مرحله برای حفظ شکل نهایی و خواص مکانیکی مطلوب، ضروری است.
پردازش نهایی
در انتها، قطعه پرس هیدرولیکی شده ممکن است نیاز به پردازشی مانند تمیزکاری، تراش و ماشینکاری داشته باشد تا به شکل نهایی خود برسد.
خمکاری (Bending)
خمکاری یک فرآیند شکلدهی فلزات و یکی از روشهای ورقکاری است که در آن قطعات فلزی از جنس آهن یا آلیاژهای آهن با استفاده از ابزارهای خمکاری تحت تنش و خمش قرار گرفته و بدون تغییر ضخامت، به شکلهای مورد نظر خم میشوند. از این فرآیند در تولید انواع قطعات و تجهیزات فلزی، از جمله قطعات خودرو، لوازم خانگی، و محصولات صنعتی استفاده میشود.
از جمله دستگاههای متداول خمکاری، میتوان به خمکاری هیدرولیک، خمکاری دستی، خمکاری برقی و خمکاری با استفاده از ماشینآلات CNC اشاره کرد. کاربرد عمدۀ روش خمکاری در شکلدهی ورقهای فلزی و ورق آهنی است. مجموعه فرداد فولاد نیز با برخورداری از دستگاه خمکاری، قادر است شکلهای مختلف را به سفارش مشتری ایجاد نماید.
انواع خمکاری آهن آلات
خم V شکل (گونیایی)
اگر از قالب و پانچ V شکل استفاده شود، اصطلاحاً خمش V به دست میآید. این نوع خمش آهنی امکان رسیدن زاویۀ گوشهها را تا 90 درجه فراهم میکند.
خم U شکل (پرسی)
هنگامی که در خمش آهن از قالبهای U شکل استفاده شده باشد، اصطلاحاً خمش U بدست میآید. این فرآیند بیشتر برای ساخت تیرها، کانالها و انواع قابها استفاده میشود. به طور مثال، ناودانی پرسی (وال پست) را میتوان به این روش از ورق آهنی ساخت.
خم فشاری
در این نوع خم شدن آهن، خمکن سطح آهن را از طریق یک استوانه یا قالب چرخشی میچرخاند. این تکنیک بیشتر برای خمهای پیچیده در صنعت ماشین آلات و قطعات استفاده میشود.
خم نورد
از این روش برای تولید لوله یا قطعات مخروطی شکل و ایجاد یک یا چند خم به طور همزمان استفاده میشود.
شکلدهی انفجاری (Explosive Forming)
روش شکلدهی انفجاری یکی از روشهای پیشرفته و کاربردی در شکلدهی فلزات است که با استفاده از انفجار و انتقال انرژی به فلز، آن را به شکل دلخواه تغییر شکل میدهد. این فرآیند برای تولید قطعات با ابعاد بزرگ و پیچیده و همچنین برای تولید قطعات با خواص مکانیکی بالا بسیار مورد استفاده قرار میگیرد. مراحل اصلی روش انفجار مکانیکی به این صورت است:
آمادهسازی ماده اولیه
ماده اولیه برای شکلدهی انفجاری باید به شکل مناسب آماده شود. این مواد معمولاً به شکل صفحات فلزی یا نوارهای فلزی آماده میشوند.
نصب ماده اولیه
ماده فلزی بر روی یک سطح صاف نصب میشود و به دقت محل نصب آن تنظیم میشود.
اعمال انرژی انفجار
در این مرحله، منبع شکلدهی انفجاری نزدیک به سطح ماده فلزی قرار میگیرد و انرژی به آن منتقل میشود. انفجار موجب اعمال فشارهای بالا بر روی فلز و شکلدهی آن میشود.
تغییر شکل و شکلدهی
شکلدهی انفجاری موجب تغییر شکل فلز گشته و به شکل دلخواهی، آن را تغییر میدهد. این فرآیند معمولاً باعث کشش، فشردگی، و یا تغییر شکلهای پیچیدهتر در فلز میشود.
پردازش نهایی
بعد از اتمام فرآیند شکلدهی انفجاری، قطعه فلزی ممکن است نیاز به فرآوری داشته باشد تا به شکل نهایی خود برسد. روش شکلدهی انفجاری به دلیل قدرت و دقت بالایی که در تغییر شکل فلزات فراهم میکند، در صنایع مختلفی مورد استفاده قرار میگیرد.
نظرات کاربران