روشهای تولید میلگرد
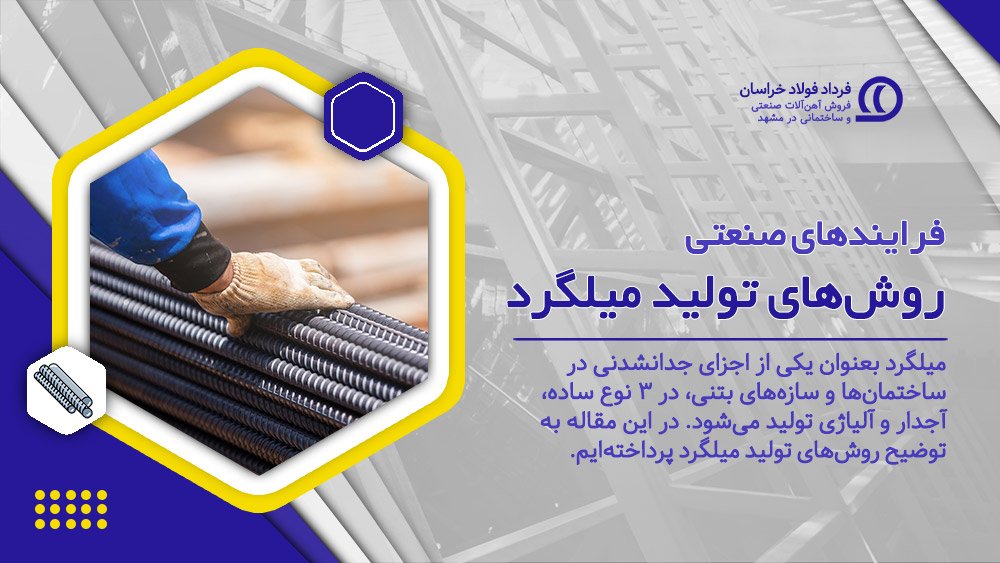
میلگرد بعنوان یکی از اجزای جدانشدنی در ساختمانها و سازههای بتنی، در 3 نوع ساده، آجدار و آلیاژی تولید میشود. در این مقاله به توضیح روشهای تولید میلگرد پرداختهایم.
میلگرد، جزء جدانشدنی ساختمان
میلگرد یکی دیگر از محصولات فولادی پرکاربرد است، که تقریبا در همه سازههای بتنی از آن استفاده میشود. میلگرد ((Rebar یک مقطع فولادی با طول زیاد، توپر و شکل استوانهای است که برخی از انواع آن، آجدار نیز هستند. میلگردها تقسیمبندیهای متفاوتی دارند که این تقسیمبندیها بر اساس نوع آلیاژ، سایز، استاندارد تولید، حالت، جنس و ... است. اما بهطور کلی، میلگردها را در سه دسته میلگرد آجدار، میلگرد ساده و میلگرد آلیاژی تقسیمبندی میکنند.
عمده کاربرد میلگرد آجدار در صنعت ساختمانسازی است؛ از آنجایی که بتن مقاومت فشاری بسیار زیادی دارد اما از نظر مقاومت کششی و پیچشی بسیار ضعیف است. قرار دادن میلگرد در بتن موجب افزایش مقاومت بتن و آسیب کمتر سازه در صورت وارد شدن فشارهای جانبی میشود.
تولید میلگرد
میلگردها بر اساس نیاز بازار و نوع سازهها تولید میشوند. از مهمترین روشهای تولید میلگرد میتوان به روش نورد گرم، روش نورد سرد، روش ترمکس (تکنولوژی(QST و روش آلیاژسازی اشاره کرد. بهطور خلاصه میتوان مراحل تولید میلگرد را به صورت زیر بیان کرد:
- گرم کردن ماده اولیه
- نورد کردن
- خنککاری قطعات نورد شده
- برش دادن قطعات در اندازههای مختلف
- بندیلبندی (بستهبندی)
نورد، عملیاتی است که طی آن ضخامت یک قطعه یا صفحه توسط غلتکهایی با اعمال نیروی فشاری کاهش مییابد. قفسه نورد مهمترین بخش خط نورد است که سطح مقطع شمش ورودی را کم نموده و طول آن را افزایش میدهد. هر یک از روشهای تولید میلگرد تفاوتهایی دارند که در ادامه به توضیح این روشها میپردازیم.
تولید میلگرد به روش نورد گرم
این روش تولیدی، رایجترین روش تولید میلگرد است. از آنجا که دمای کاری در این روش در حدود 800 تا 1200 درجه سانتیگراد است، به آن نورد گرم میگویند. در روش نورد گرم ابتدا شمشهایی فولادی را تا دمای نرم شدن آنها که در حدود 900 تا 1100 درجه است در کورههایی مخصوص گرما میدهند. این کار به شکلپذیری راحتتر شمشها کمک میکند. سپس این شمشهای نرم شده وارد فرآیند نورد میشوند.
در فرآیند نورد، غلتکهایی با چینش 4 و 8 وجهی وجود دارد که در خلاف جهت هم میچرخند. شمشها دو مرحلۀ عبور از غلتک چهار وجهی و سپس عبور از غلتک هشت وجهی را میگذرانند که در نهایت و در سومین مرحله، به سطح مقطع دایرهای و با قطر مناسب میرسند. طی این عملیات قطر شمش فولادی کم گشته و طول آن افزایش پیدا میکند که به این عملیات اصطلاحاً "رافینگ" گفته میشود.
اندازهبندی و آجزنی
بعد از اینکه میلگرد به قطر مناسب رسید، وارد مرحله بعدی قفسه میشود که در این مرحله، خروجیهای متفاوتی از میلگردها با قطرهای مختلف خواهیم داشت. برای تولید میلگردهای آجدار یک مرحله دیگری هم باید گذرانده شود و آن هم مرحله آجزنی است که با توجه به استانداردهای لازم و طبق نیاز، انجام میشود. براساس استاندارد، آج یا بهطور مستقیم در خط نورد ایجاد شده و یا بعد از خنکسازی میلگرد با آب تا دمای محیط، انجام میشود.
در انتها میلگردهای تولید شده وارد فرآیند برش شده و در طولهای مورد نیاز برش داده میشوند. به طور معمول، طول میلگردها بین 24 تا 36 متر است. البته طول میلگردهای موجود در بازار مصرفی طبق استانداردهای بینالمللی و ملی معمولاً از 12 متر بیشتر نمیشود.
تولید میلگرد به روش نورد سرد
این روش تولید میلگرد تا مرحله قفسۀ اولیه (رافینگ) که هدف آن کوچک و دایرهای کردن سطح مقطع شمش فولادی است، با روش نورد گرم مشترک است. اما در نورد سرد، شمش بعد از مرحله رافینگ وارد مرحله متفاوتی نسبت به نورد گرم شده و آن مرحله، خنککاری است که در طی آن شمش خنک و سرد میشود. بعد از خنککاری، دوباره فرآیند تولید مشابه نورد گرم است.
اما در نورد سرد، میلگرد باید مراحل بیشتری از نورد را بگذراند و تعداد غلتکهای مورد استفاده در نورد بسیار بیشتر است؛ زیرا در نورد سرد، شمش به اندازه نورد گرم نرم و شکلپذیر نیست و شکل دادن به آن کار بسیار سختتری است. با وجود اینکه میلگرد تولیدی در نورد سرد مقاومت و سختی بیشتری (نسبت به روش نورد گرم) دارد، اما شکلپذیری، مقاومت کششی و مقاومت پیچشی کمتری داشته و همین ویژگیها باعث میشود که این نوع میلگرد، برای مناطق زلزلهخیز مناسب نباشد.
تولید میلگرد به روش ترمکس (تکنولوژیQST)
فرایند Quenched and Self-Tempered که به آن به طور مختصر"QST" میگویند، یک فناوری تولید میلگرد است که معنی لغوی آن "خودآبدیده" یا "فرونشسته" است. در سال های 1970 تا 1990 میلادی این روش برای افزایش استحکام میلگردها و امکان ساختوساز راحتتر آسمانخراشها و به درخواست مهندسین عمران ابداع شد.
بعد از فراگیر شدن این فناوری، روش QST توسط کارخانهای در هندوستان بهینهسازی شده و نام تجاری آن ترمکس (THERMEX) گذاشته شد. در سرتاسر جهان، تولیدکنندگان میلگرد ترمکس حرف T انگلیسی را روی آن حک میکنند تا خریداران از نوع آن آگاه شوند.
فرایند ترمکس
مراحل ساخت این نوع میلگرد تقریبا مانند روش نوردگرم است، بدین صورت که میلگرد خروجی در روش نورد گرم (با دمایی در حدود 930 تا 1060 درجه) تحت شرایطی کنترل شده و در محفظهای مخصوص سردسازی، توسط جریان آب و یا با استفاده از روغن، سرد میشود. اما میلگرد به روشی مخصوص سرد میشود، بهطوری که سطح میلگرد سرد گشته ولی مرکز آن همچنان داغ میماند.
در این حالت به دلیل سردسازی سریع سطح میلگرد، ساختار کریستالی سطح تغییر کرده و سطح آن سخت و شکننده میشود؛ اما مرکز آن نرم و انعطافپذیر باقی میماند. سپس میلگردها از بخش سردکننده بیرون آورده شده و روی صفحههایی (صفحه خنککننده) در معرض هوا قرار میگیرد. در این شرایط، گرمای مرکز میلگرد به سطح آن منتقل شده و در نتیجه، مجدداً ساختار سطح میلگرد تغییر کرده و چقرمگی جای شکنندگی را میگیرد.
تفاوت با روش نورد گرم
در نتیجه این نوع میلگرد سختی سطح بالا، امکان جوشکاری مناسب، نقطه تسلیم بالا و همچنین چکشخواری بالاتری دارد. البته موارد گفته شده تنها تفاوتهای روش ترمکس و نورد گرم نیست. از دیگر تفاوتها، میتوان به تفاوت ترکیب آلیاژی این دو روش اشاره کرد. به این معنا که کربن آلیاژ مورد استفاده در روش ترمکس کمتر است و در نتیجه هزینههای تولیدی نسبت به روش نورد گرم بسیار کمتر است.
میلگرد TMT
نکته قابل توجه دیگر اینکه میلگرد TMT همان میلگردی است که با تکنولوژی QST ساخته شده، اما تحت لایسنس THERMEX تولید نشده است. این نوع میلگرد برای مناطقی که زلزلهخیز نیستند بسیار کاربردی است. مثلا در اکثر کشورهایی اروپایی که از نظر زلزله مناطقی امن و بدون زلزله هستند، این روش تولیدی یک روش بسیار ایدئال ، مقرون به صرفه، سریع و عالی است.
تولید میلگرد به روش آلیاژسازی
این روش نیز همانند روش نورد گرم است. تفاوت آن با نورد گرم مربوط به مراحل ابتدایی یا همان مرحله تولید شمش فولادی است. فولاد مورد استفاده در روش آلیاژی از همان ابتدا با ترکیب فروآلیاژها (ترکیب آهن و عناصر دیگر) ساخته میشود؛ به این صورت که عناصری مانند وانادیوم، نیوبیوم، تیتانیوم و ... را به فولاد اضافه میکنند و در نتیجه، خواص فیزیکی و مکانیکی میلگرد به طور چشمگیری تقویت میشود.
از آنجایی که در این روش میلگردها بعد از تمام شدن فرآِیند تولید در معرض هوا خنک و سرد میشوند، بنابراین خواص فیزیکی میلگرد از مرکر تا سطح یکسان است. این روش برای ساخت میلگرد با خواص سفارشی کاملا مناسب است.
از آنجایی که این نوع میلگرد مقاومت، استحکام کششی و پیچشی مناسبی دارد، پس برای مناطق زلزلهخیز بسیار مناسب است؛ به همین دلیل است که در کشورهای زلزلهخیز مثل ژاپن، از این روش برای تولید میلگرد استفاده میشود.
بهترین میلگرد برای ایران کدام است؟
بهطور کلی از آنجایی که در کشور ما اقلیمهای متفاوتی وجود دارد و ویژگیهای هر منطقه با منطقه دیگر متفاوت است، بهتر است که براساس ویژگیهای هر منطقه، از روش خاصی برای ساخت میلگردها استفاده کنیم. در ایران، ما هم مناطق زلزلهخیز و هم مناطق امن داریم مثلا کرمانشاه شهری بسیار زلزلهخیز است ولی خطر زلزله در اصفهان بسیار کم است. به همین دلیل است که در ایران از هر دو روش آلیاژی و ترمکس برای تولید میلگرد استفاده میشود.
به همین منظور سازمان استاندارد ایران، استاندارد میلگرد ایران با نام کوتاه شده ISIRI 3132 را ارائه داده است. استاندارد 3132 ترکیبی از چند استاندارد بینالمللی و الهام گرفته از استانداردهای زیر است:
- استاندارد DIN (آلمان)
- استاندارد GOST (روسیه)
- استاندارد JIS (ژاپن)
- استاندارد ASTM(آمریکا)
نظرات کاربران